Motorbike Frame Tube Thickeness
Today, Pearlite Steel will discuss about the key difference between Seamless and ERW Stainless Steel Pipe What is the Raw material required for manufacturing Seamless & ERW Stainless steel Pipes?Seamless Steel Pipe is made from a solid round steel ‘billet’ which is heated and pushed or pulled over a form until the steel is shaped into a hollow tube. Billets are procured both from indigenous suppliers and from abroad. Major Indigenous suppliers are JSPL, JSW & Kalyani and steel round billets are imported from renowned mills from Europe, Far East countries, Canada, China.To Manufacture ERW Stainless Steel Pipes HR Coils are required. Major Indigenous suppliers of these HR Coils are SAIL, Essar, JSW, Lloyds etc.What is the Difference Between Seamless and ERW Stainless Steel Pipes?Electric Resistance Welding (ERW) pipe is manufactured by rolling metal and then welding it longitudinally across its length. Seamless pipe is manufactured by extruding the metal to the desired length; therefore ERW pipe have a welded joint in its cross-section, while seamless pipe does not have any joint in its cross-section through-out its length.In Seamless pipe, there are no welding or joints and is manufactured from solid round billets. The seamless pipe is finished to dimensional and wall thickness specifications in sizes from 1/8 inch to 26 inch OD.
Applicable in for High-pressure applications such as Hydrocarbon Industries & Refineries, Oil & Gas Exploration & Drilling, Oil & Gas Transportation and Air and Hydraulic cylinders, Bearings, Boilers, Automobilesetc.ERW (Electric Resistance Welded) pipes are welded longitudinally, manufactured from Strip / Coil and can be manufactured upto 24” OD. ERW pipe cold formed from a ribbon of steel pulled through a series of rollers and formed into a tube which is fused through a electric charge. It is mainly used for low/ medium pressure applications such as transportation of water / oil. Pearlites steel is one of the leading ERW Stainless Steel Pipes Manufacturer and exporter from India. Contact us for product details.Common sizes for ERW Steel Pipe range from 2 3/8 inch OD to 24 inch OD in a variety of lengths to over 100 feet.
Surface finishes are available in bare and coated formats and processing can be handled on site to customer specifications.What Technologies are used to manufacture Seamless & ERW Pipes?Technologies for Production of Seamless & ERW Pipes “CPE” Technology” used for Seamless Pipes & Tubes Production up to 7-inches OD is the world renowned Technology. “Plug Mill” Technology used for Higher Dia. Seamless Pipes & Tubes Production from 7-inches to 14-inches,is the most reliable technology,in higher dia. High frequency Induction Welding Technology is used for ERW Pipes &Tubes upto 21-inchesOD.How to Identify Seamless or ERW Stainless Steel pipes?To identify that a pipe supplied is seamless or ERW, Simply read the stencil on the side of the pipeIf it is ASTM A53, Type S means seamless.Type F is furnace but welded,Type E is Electrical resist welded.Thats how. It is the easiest way to identify wether pipe is seamless or ERW.In short, Seamless is marketed on an outdated myth that it does not have flaws but that welded has an inherent flaw throughout the length of each tube, as stated above. Intuitively this concept is easily accepted by purchasers and designers with limited experience with the various products. Each product form and manufacturing method has its own inherent problems and potential defects.Consumers must become familiar with what those problems and defects are, and how they might affect particular applications.
Then they can make an informed decision based on facts, rather than myth.Let’s see the video of ERW Stainless Steel Manufacturing Process.Pearlite Steel is one of the leading manufacturers and exporters of ERW Stainless Steel pipes from India. We manufacture ERW steel pipes in various dimentions and shapes. We are also one of the largest Stainless Steel pipes exporter from India, our manufacturing unit is situated at Rajkot, Gujarat (India). We use the finest quality of raw material to produce SS pipes, which ISO and OHSAS certified. Our Stainless Steel manufacturing unit is capable of producing large and customized order from our client around the world. Skype or Mail us for more information about our ERW stainless Steel pipes. Stainless steel pipe supplier from Gujarat.
Stainless Steel pipe exporter from India.Pearlite steel – Stainless Steel pipe Manufacturer from India.
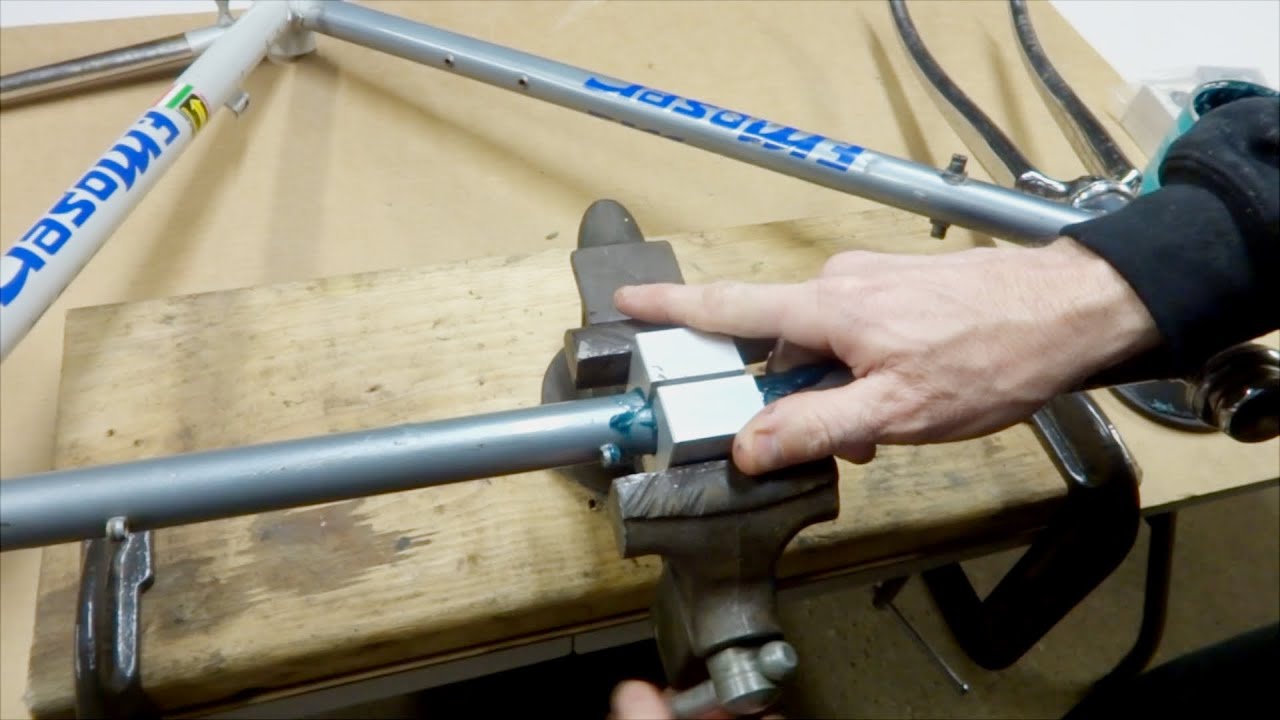
(As seen in the Welding Journal, October 2005)Tommy Scott sits atop the chopper he built. Although he's a professional mechanic who uses welding in his everyday job, a project such as this is within the reach of many do-it-yourselfers if they have the right equipment and tube welding knowledge.If shows such as American Chopper have you dreaming of cruising down the road on your own custom bike, you're certainly not alone. Each week, millions of people tune in to watch the sparks fly (from both the metal and the stars) and learn the secrets of the pros.
Not content to just watch, an increasing number of people want to turn their garages into home fabrication shops. If you're considering that, now comes your dilemma: Which process do you use for welding the tubing that forms the frame?Of all the welding process available, the gas metal arc welding (GMA) and gas tungsten arc (GTA) welding processes are best suited for welding tubing of a motorcycle frame. Many frames are GMA welded, and GMAW is the easiest process in which to become proficient - Fig.
While GTAW requires more coordination, it allows for more control, particularly in tubing applications. The attraction of the GTAW process may prompt those who gas metal arc weld professionally to further expand their skills and learn GTAW.
1 - With training, even beginning operators will be able to lay beads that look like this with the GMAW process. Keep in mind, however, that you must use sufficient amperage for the application so that your great-looking GMA weld is also a good-quality weld.To help you determine which process best meets your needs, let's compare and contrast elements of the GMAW and GTAW processes specifically as they relate to welding tubing in a home-fabrication setting. Before that, we need to talk about the type of metal you'll be welding and some basic setup and safety information.The MetalMany professional fabricators choose drawn-over-mandrel (DOM) steel tubing for the frame material. According to the Steel Tubing Institute, 'DOM refers to high-strength, electrically welded tubing that has been further processed by cold drawing through dies and over mandrels to improve its uniformity, mechanical properties and surface finish. Because of its many advantages, DOM is the material of choice in many of the most demanding applications for tubing.' Drawn-over mandrel tubing is produced to more exact outside and inside dimension tolerances, has a better finish without seams, and is widely used in high-stress applications requiring higher quality, uniformity, strength, and soundness such as a motorcycle frame and the frames used to build many other motorsports vehicles (stock cars, dune buggies, etc.).Drawn-over mandrel tubing is manufactured to ASTM Specification A513 Type 5, and frame fabricators often chose SAE Steel Grades 1018 and 1020. These have a yield strength of 70 ksi or 483 N/mm2.
You can find them at a local metal supplier and at many online stores. Most tubing on a bike has a 11⁄8- to 11⁄2-in. OD and a 0.120-in. Wall thickness, except for the steering neck tube, which is larger and thicker (perhaps 0.250 in. Thick) - Fig. 2 - Scott uses a 250-A GMAW machine to weld the chopper's neck. This area calls for larger, thicker tubing (perhaps 0.250 in.
Motorbike Frame Tube Thickness Chart
Thick) than the rest of the bike.Considerations before WeldingFor best results, buy or build a jig for the bike frame. While building a jig consumes time, it will help ensure that each piece of the frame fits perfectly into the bike's design.
It also acts as a valuable third hand and leads to better weld quality - Fig. Simply stated, poor fitup often leads to poor welds. Many motorcycle frame and component suppliers offer jigs or plans for them that correspond with the frame plans they sell. An online search will yield many sources.There is one additional thing you need to do before you can start welding: read the owner's manual for your welding machine and follow all safety precautions. This includes creating a well-ventilated work area free from potentially combustible materials, and wearing welding-safe clothing, including an autodarkening or fixed shade welding helmet, long pants, closed-toe shoes, protective welding leathers, and gloves.
These practices ensure the safest, most effective welding experience.Fig. 3 - A jig traps the frame at all points.Why GMAW?Gas metal arc welding is used at all levels of metal fabrication. It is an easy process to learn, and can weld mild steel, stainless steel, and aluminum, as well as thin to thick materials. In addition, travel speeds are usually faster with GMAW because welding wire is continuously being added to the joint.However, in small-diameter tubing applications, faster travel speeds can hinder your ability to control the weld bead profile and appearance. Once set,voltage and wire feed speed parameters remain constant. As a result, when you're trying to weld around the circumference of a tube, it is difficult to stay on the leading edge of the molten pool.
You need to continually reposition your body to maintain a proper gun angle and to direct the arc at the leading edge of the weld pool. Unfortunately, if this is not maintained, the result could be incomplete fusion at the toes of the weld or incomplete penetration at the root of the weld.To compensate, some people might want to use a lower voltage and slower wire feed speed. This will make it easier to manipulate the gun and control the shape of the weld bead, but beware: With GMAW, beauty is only skin deep.
You can have a great looking GMA weld, but if your parameters were set too low for the material thickness, then the weld just rests on top of the base metal and fails to achieve good penetration. In short, you must use sufficient amperage for the application.You'll also want to consider how position will affect the strength of the weld. Welding in the downhill position can be like riding on the top of an avalanche.
While it may be faster and easier to weld in this position, the filler metal could ride on top of the weld pool, dramatically increasing the risk of poor fusion and/or penetration and is not recommended. The contour of the weld may also be concave, which in turn may cause the throat of the weld to be too narrow, producing a weak weld. Filler Metal, Shielding Gas, and NozzlesFor tubing with a 0.120-in. Victoria 2 papal states 3. Wall thickness, a good welding wire is a 0.030- or 0.035-in.-diameter, S-6 hard wire (American Welding Society classification ER70S-6).Use a 75% argon/25% CO2 shielding gas. Compared to 100% CO2, this mix yields smooth arc characteristics, better pool control, good bead wetting action, good bead control, and less spatter. It also reduces the chance of melt-through on thinner materials because it requires less voltage and lower wire feed speeds than straight CO2.
Flow rates are typically around 30 ft3/h.Shielding gas nozzles also need to be monitored, cleaned, and occasionally replaced. Depending on the nozzle size and its workload, spatter can build up and impede the proper flow of shielding gas and leave the weld pool unprotected.
GMAW TechniquesTo get better starts, some welders will clip the ball off the end of the weld wire. This ensures a better, hotter start when beginning at the end of a previous weld.
When ready to weld, there are two methods to use. One is the push or forehand method that involves pushing the gun away from the weld pool. This produces somewhat less penetration for a given amperage and a wider, flatter bead. It also makes it easier to keep the arc on the leading edge of the pool to ensure good penetration (compared to the drag or backhand method), which is why it is recommended for welding tubing.While moving the gun forward consistently produces a sound weld with decent appearance, some people like the appearance of an overlapping bead profile, which is sometimes referred to as the 'stack of dimes' look. This takes practice.The 'stack of dimes' look can be achieved a couple of ways. One is through a forward or push movement of the gun, then a slight back step or hesitation, and then moving forward again. Another method is using an overlapping 'C' motion of the gun.
This produces the 'CCCCC' look of stacked dimes. Remember to make your individual beads close together. If they are too far apart, to the point where the toes of the weld become widely separated, the weld can fracture at any of those indent points (stress risers and/or crater cracking). Note that on 0.120-in.-wall tubing, melt-through and/or warping may occur if you make too long of a weld bead using this technique. To minimize heat input, make several short welds rather than one long one. Also, consider skipping around a frame, making a short, partial weld on one joint and then moving to a different part of the frame. This gives the weld a chance to cool.
Why GTAW?Gas tungsten arc welding is the solution for more weld control and precision. It allows you to weld thinner material, provides excellent fusion, and solves problems related to melt-through or warping that are more common in GMAW. Gas tungsten arc welding also produces the best-looking weld beads. This is important when appearance really counts, and, unlike with GMAW, the good news is that beauty goes clear to the root of the joint, If your GTAW bead looks good, chances are the weld is strong.Gas tungsten arc welding, especially in tubing applications, helps overcome some of the drawbacks of GMAW. Instead of needing to maintain a consistent travel speed or risk incomplete fusion, GTAW lets you control the heat input with a foot or hand control in reaction to the changing dynamics of the molten weld pool.
This gives you more control over the shape of the weld bead, penetration, and HAZ.But taking control requires more coordination. You're doing four different things at once: holding your torch with your right or left hand, holding the filler metal in your opposite hand, using your foot control, and watching the joint and the weld pool. It is extremely important to make sure your arms and elbows are braced yet relaxed (this is true with GMAW also, but especially with GTAW). Note that you want to establish the weld pool as quickly as possible. Dwelling too long in one spot increases the size of the HAZ, which is undesirable.Selecting Tungsten, Welding Wire, and CupsSelect a 1⁄16-in.-diameter tungsten (2% thoriated, 2% ceriated, or 1.5% lanthenated) for the best results with the material thickness used for motorcycle frames. A good rule is to use the smallest electrode that will carry the right amount of current and give you the proper pool size.

On 0.120-in.-wall tubing, 1⁄8-in. Tungsten can create a weld bead that is too wide.Choose a 3⁄32-in. Welding wire because it will melt at the optimum amperages for welding 0.120-in.-wall tubing, as well as produce a bead width that is most compatible with this wall thickness. Anything larger will require more heat to melt, which may result in melt-through.A #6 or #7 GTAW cup is standard in this type of application. A gas lens will give you much better shielding of the whole area and allow for further tungsten extention, which will help when welding included angles. Using 100% argon, flow rates are typically 15 to 20 ft3/h, and remember that more is not better no matter what your welding process.
Excessive flow rates can create turbulence and induce porosity in the weld. GTAW TechniquesWhen performed correctly, GTAW naturally produces the overlapping bead profile, or 'stack of dimes' look. The shielding area, proper cup size, and gas lens are crucial to good GTA welding, but torch angle is probably the biggest factor.Angling the cup back (you always 'push' the torch when GTA welding) preheats the metal in front of the pool. Gas tungsten arc welding requires a balancing act between developing the right torch angle, adding your filler metal, and amperage control. If you angle the torch too far back, the heat is going to be far out in front of the pool and you will need to reduce current levels to compensate for the heated metal in front. While torch angles change depending on position and application, for welding on tubing, pull the torch back at an angle of about 70 deg (and, of course, maintain a proper angle of 45 deg with respect to the two components of the joint).Continually changing angles to accommodate for the geometry of the tube is the greatest obstacle to sound, attractive GTA welds.
It requires tremendous time, patience, and operator skill to create quality welds under these conditions. Practice first.A more nontraditional GTAW technique, called cup walking, involves resting the GTAW torch right on the tubing with the filler metal placed in the groove of the weld. This technique provides more arc stability and greater comfort, while also allowing the operator to change positions more easily. More information on cup walking can be found in the June 2005 issue of the Welding Journal.Fig.
4 - Whether you use GMAW or GTAW, you probably will not be able to travel all the way around the tube with a consistent gun or torch angle. Good advice is to make four welds on a tube, 90 deg at a time, such as is shown in this GTA weld.Four-Bead Joint: GMAW and GTAW AdviceIt will be necessary to start and stop while going around the tube. Most people will not have the ability to start and go all the way around the tube with a consistent torch angle. Those who try start with one angle on the gun/torch and end up pushing it as the gun/torch rotates around the tube. This changes the bead profile and penetration. A better technique is to make four welds on a tube, 90 deg at a time.
Start on one side, repeat on opposite side, and tie the two together - Fig. As an added benefit, you alternate the heat input, creating less stress on one side of the tube, which will help keep the frame square.To achieve good tie-in between all weld beads, start just on top of the last weld you made to get the previous weld bead 'dime' molten. This helps ensure the hotter part of the 'running' arc will tie in the already-welded area of the tubing. Another option is to start the arc by directing the electrode at the root of the joint, quickly backstepping into the previous weld bead, then traveling forward and welding over your arc start and remelting it. Because a cold start can be a weak spot, you may even want to borrow a technique common in pipe welding: grind out your start and stop points. If you're gas metal arc welding, also consider grinding out your tack welds (GTAW tacks should be smaller and thus will be readily consumed when welding).Fig. 5 - For out-of-position welds on tubing, weldng in the uphill position can provide more consistent heat control and better weld penetration.For out-of-position welds on tubing (a fact of life because the frame will be fixed in a jig), welding in the uphill position will provide more consistent heat control and better penetration - Fig.
Start at 6 o'clock and work your way up to the 12 o'clock position. Welding uphill may take longer because gravity pulls the bead down, but this ensures that you have a better chance at keeping the arc on the leading edge of the pool, which achieves good penetration at the root of the joint and good sidewall fusion. Note that it may be necessary to add a slight side-to-side weave or 'C' motion to control the size and shape of the bead, as well as to allow it to cool slightly.Note that the weave should not need to be too wide. If it is, that indicates a wide root opening as the result of poor fitup.
While GMAW lets you bridge gaps more easily than GTAW, bridging gaps is not a good idea when welding critical structures like a motorcycle frame. The gap may likely create a joint with insufficient mechanical strength, or, because you dwelled on the joint longer to fill the gap, create an excessively wide HAZ, or even melt-through.Fig. 6 - Good fitup is crucial to making quality gas tungsten arc welds.
At left is an example of good fitup; poor fitup is shown at right.Gas tungsten arc welding really requires tight fitup because you need to develop the weld pool and establish a bond between the two sides before you add filler metal - Fig. If you have a gap, it becomes very difficult to bond the two sides because it's easy to put too much heat into one side.
Compensating for this imbalance often results in excess heat and subsequent melt-through. For both processes, if you have a small gap, focus on the edges, tie-in each side and pause for a moment.
For wider gaps, throw the part in the scrap bucket and cut a part that fits properly. Remember: You can't weld air. Defects and TestingSome welds are doomed to failure from the start because of poor preparation. Clean any surface prior to welding, using a wire brush, grinder, and/or solvent to remove rust, mill scale, paint, oil, or any other foreign substance that will inhibit maximum penetration and lead to weld failure.That said, the most common welding defects that occur in both GMAW and GTAW are incomplete fusion at the edge, or toe, of the weld and incomplete penetration at the root of the joint. These defects, as we've noted, result from poor techniques or improper settings.Porosity, caused by atmospheric contamination, insufficient gas coverage, or base metal contamination, is also a common discontinuity that could eventually cause cracks. If you notice porosity or cracks, it may not be a good idea to grind it out and reweld it, because you risk increasing the HAZ.
Bike Frame Tube Thickness
The more you heat steel, the more you change the temper of it.A good first test to uncover welding defects is a visual test. You should see good wet-out and tie-in at the toes of the weld, and the bead should have a fairly consistent appearance. If you see areas with an irregular bead profile or an excessively high crown, you could have a weld defect. Your weld should be flat to convex (not too high), but it should never be concave.Lastly, a weld should look balanced on either side of the root of the joint. Misalignment occurs when you weld more to one side than the other, creating asymmetry through the joint.
On any joint, each leg of the weld bead needs to be at least as long as the wall thickness of the base material (e.g., this ensures that the weld will not be the proverbial 'weakest link in the chain'). For 0.120-in.-wall tubing, each leg of the weld bead needs to be 0.120 in. Varying from this symmetry could create a defective weld, one that's weak at one point and overwelded at the other.Another nondestructive but effective and inexpensive method for finding surface defects is dye penetrant testing. After cleaning the surface, spray dye on the metal, let it sit per manufacturer's instructions, clean it off, and put an emulsifier on. The emulsifier will pull the dye out of any voids it seeped into. If you made a void-free weld, you won't see any dye.Destructive testing involves imposing a force on the metal, such as putting it in a vice and hitting it with a hammer, to see if the metal bends before the weld breaks.
Chopper Builders Handbook
If the weld bead is holding and it's tearing at the base metal, your weld is at least as strong as the base metal. The heat-affected zone should be the weakest link.Most importantly, once you produce structurally sound welds, document your welding parameters and practice extensively on the actual joints you'll be welding. With practice, you can be confident that when it comes time to weld your motorcycle, you will create quality welds time and time again. To activate your FREE subscription today, simply select which newsletter(s) you would like to receive and complete the form below.Miller respects your privacy concerns. Read our for more information.Already signed up? Manage your subscription(s) by signing into your account. Or if you don't have a Miller account, create one today.Please select at least one e-Newsletter.DIY.PRO.INSTRUCTOR.WELDING SAFETY.PROMOTIONAL EMAILS.THE BEVEL.First Name.Last Name.Email Address.Confirm Email.Country.Postal Code.